With the continuous advancement of technology, industrial chillers have found increasingly widespread applications in various industrial fields. They play a crucial role in ensuring the efficient operation of industrial production and enhancing product quality. However, as mechanical equipment, industrial chillers are inevitably prone to certain issues during long - term operation. One of the common problems is equipment corrosion. To effectively prevent the corrosion of industrial chillers and extend their service life, Hengde Company elaborates on the six major common causes of chiller corrosion and provides corresponding preventive measures.
1. Corrosion Issues Caused by Unreasonable Engineering Construction, Design, and Installation
Some factories, especially when selling ordinary industrial chillers, cut corners to reduce costs and neglect essential anti - corrosion and anti - rust treatments. Once customers expose the chiller to the outdoor environment for an extended period, the equipment shell is highly susceptible to corrosion. This corrosion risk resulting from the neglect of anti - corrosion measures in the early construction and installation stages can severely affect the normal operation and service life of the chiller.
Preventive Measures: When purchasing equipment, choose suppliers with good reputations and quality guarantees to ensure that the chiller has undergone comprehensive anti - corrosion and anti - rust treatments before leaving the factory, such as spraying high - quality anti - corrosion paint and using corrosion - resistant materials for the shell. Before installation, assess the installation environment and avoid placing the equipment in humid, dusty, or corrosive gas environments. If outdoor installation is unavoidable, build a protective shed to shield the equipment.
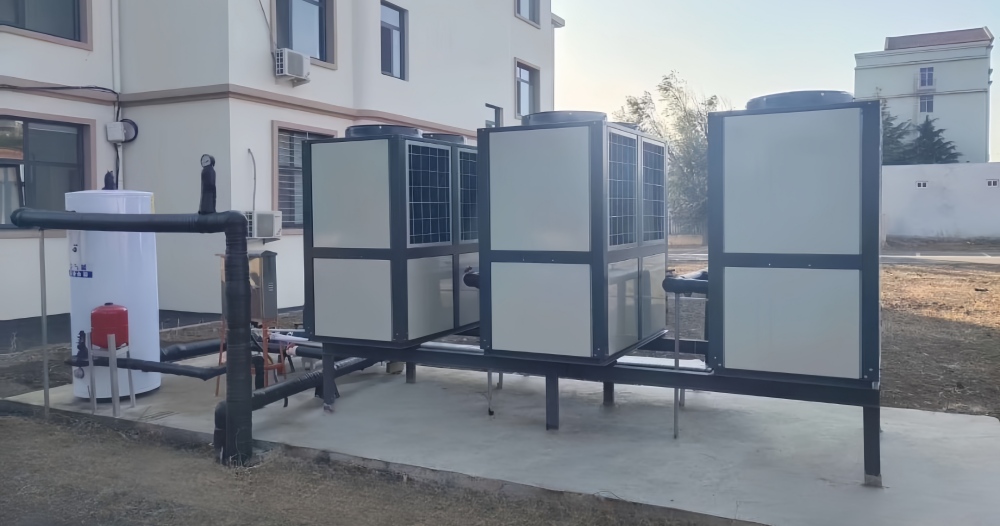
2. System Pipeline Corrosion Caused by Incorrect Installation or Abnormal Operation of the Water Processor
In water cooled chillers, the cooling water pipeline is a key passage for cooling water circulation. The quality of the water directly determines whether scale and rust will form in the system pipelines. If the water processor is installed improperly or operates abnormally, it cannot effectively treat the water quality, thereby triggering pipeline rust. This not only reduces the heat exchange efficiency of the chiller but may also lead to pipeline blockages, affecting the stable operation of the entire system.
Preventive Measures: Before installing the water processor, strictly follow the product manual for correct installation and conduct debugging after installation to ensure its normal operation. Regularly maintain and service the water processor, checking whether all its functions, such as filtration, sterilization, and descaling, are normal. Meanwhile, regularly test the cooling water quality and adjust the operating parameters of the water processor or replace consumables like filter elements in a timely manner according to the water quality conditions.
3. Insufficient Filtration of Fine Impurities by Y - type Filters
Currently, the commonly used dirt removers in industrial chillers are mostly Y - type filters. They have the advantages of easy installation and convenient dirt cleaning and can conduct preliminary rough filtration of mechanical impurities, iron filings, and sand grains. However, their filtration effect on tiny impurities is unsatisfactory. As the unit operates for a long time, the condenser is extremely likely to accumulate dirt, sludge, and other impurities. These deposits not only reduce the heat transfer performance of the condenser but may also accelerate the equipment's corrosion process due to the formation of a local corrosion environment.
Preventive Measures: Based on the Y - type filter, add a precision filter to conduct more refined filtration of tiny impurities. Regularly clean and maintain the Y - type filter and the precision filter, and promptly remove the impurities inside the filters. At the same time, regularly clean the condenser. Chemical cleaning or physical cleaning methods can be used to remove the dirt and deposits inside the condenser and maintain its good heat transfer performance.
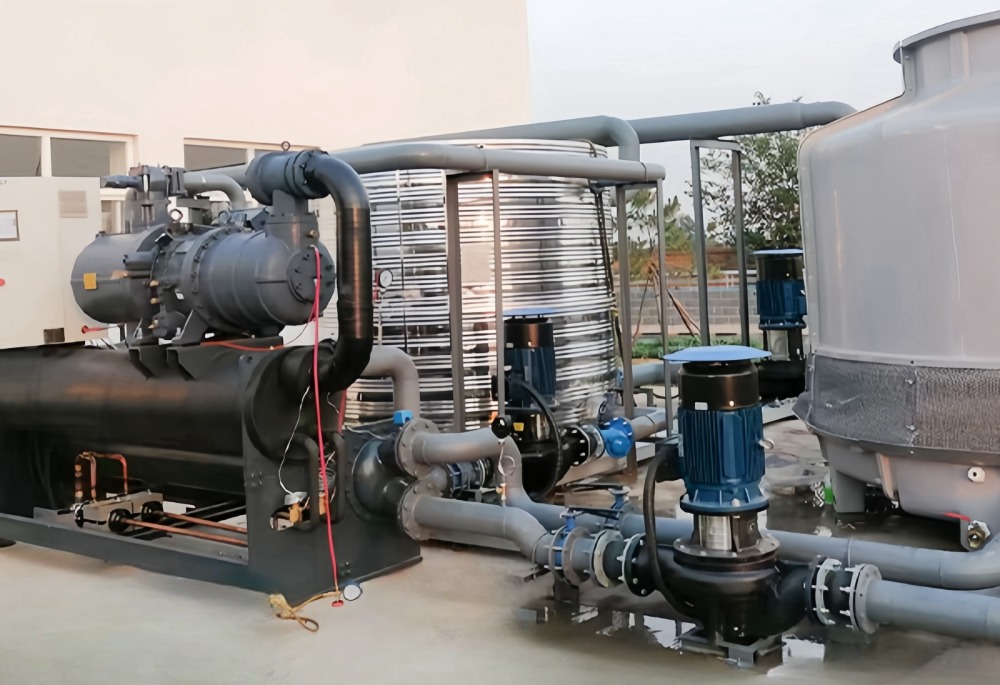
4. Absence of a Quick Drain Valve in the Chilled Water System
The quick drain valve plays an important role in draining in the chiller or chilled water system. It has a simple structure, good sealing performance, small size, and light weight, and is especially suitable for regular draining of the system. It also has the advantages of corrosion resistance, impact resistance, and long service life. However, currently, many industrial chiller end plates in enterprises do not have a quick drain valve installed, which is likely to cause system pipeline corrosion. During the daily operation of the chiller, it is recommended to open and close the drain valve three times a week to ensure smooth system drainage and maintain the good operation of the system.
Preventive Measures: For chilled water systems that have not installed a quick drain valve, install a quick drain valve that meets the system requirements as soon as possible. In daily use, strictly follow the recommended operation frequency to open and close the drain valve to ensure that impurities and dirt in the system are discharged in a timely manner. At the same time, regularly check the sealing performance and working status of the drain valve and replace it promptly if it is damaged.
5. Absence of a Water Meter in the Cooling System Makeup Water Pipeline
In the water quality treatment process of the cooling system, chemicals and bactericides are usually used to kill fungi, microorganisms, and remove various dirt inside the pipeline. The dosage of the chemicals needs to be accurately adjusted according to the makeup water volume and the system water volume. If there is no water meter installed in the cooling system makeup water pipeline, it is impossible to accurately measure the makeup water volume, resulting in inaccurate chemical dosing. Excessive dosing may cause chemical corrosion of the pipeline, while insufficient dosing cannot effectively inhibit the growth of microorganisms and the formation of dirt, also triggering system pipeline corrosion problems.
Preventive Measures: Install a water meter with appropriate accuracy in the cooling system makeup water pipeline to accurately measure the makeup water volume. According to the system water volume and makeup water volume, accurately calculate the dosage of the chemicals according to the chemical usage instructions. At the same time, regularly test the water quality of the cooling system and adjust the dosage and type of the chemicals in a timely manner according to the test results to ensure that the water quality is in a good state.
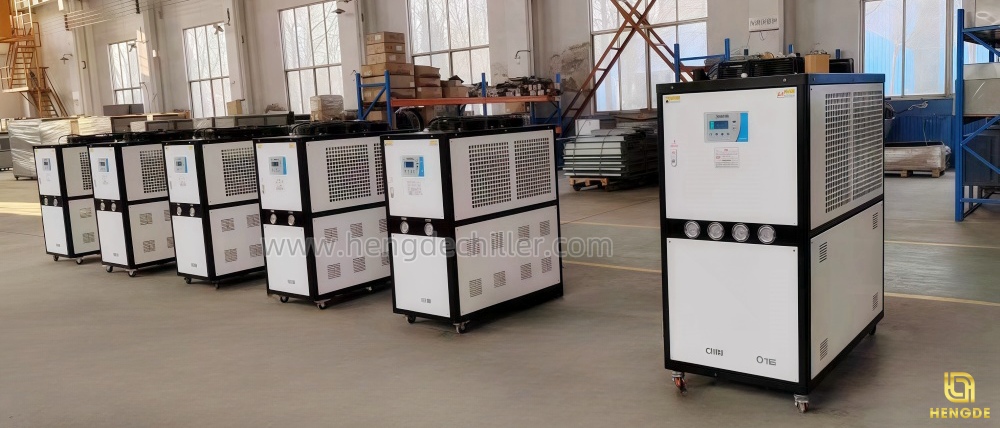
6. Corrosion of the Equipment Surface by Acidic and Alkaline Gases in the Environment
During factory production, some special gases, such as acidic and alkaline gases, are inevitably generated. These gases flowing in the environment can cause erosion damage to the equipment surface. Therefore, when selecting a chiller in an environment with such special gases, it is necessary to explain the situation in detail to professionals in advance so that explosion - proof and corrosion - resistant materials are preferentially selected for the production of the electrical control box or evaporator pipeline. This can effectively prevent the equipment from being corroded and damaged by acidic and alkaline gases during the later operation.
Preventive Measures: During the equipment selection stage, fully consider the gas components and concentrations in the working environment and choose chillers with corresponding protection levels and corrosion - resistant properties. For installed equipment, gas purification devices can be set up around the equipment to reduce the concentration of acidic and alkaline gases in the environment. Regularly inspect and maintain the equipment surface. If there are signs of corrosion, promptly carry out repair and protection treatments, such as repainting anti - corrosion paint.
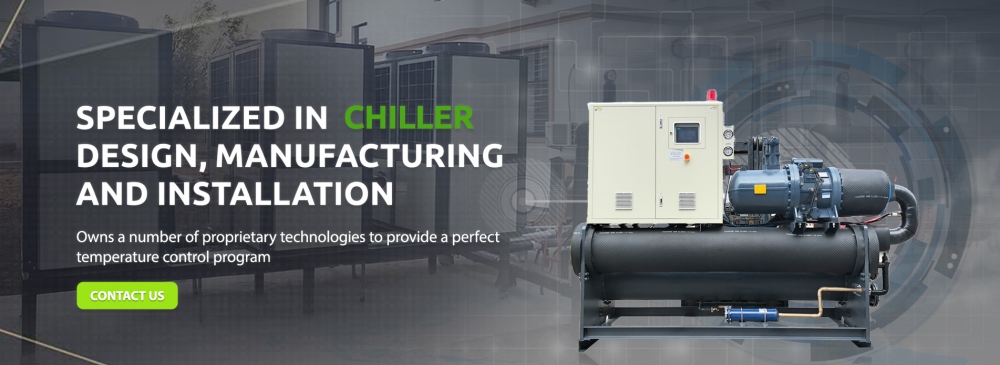
With the rapid development of industry and the continuous emergence of new materials and new processes, the application scenarios of industrial chillers are becoming increasingly diverse, which increases the risk of equipment corrosion. Here, Hengde earnestly reminds industry friends that for industrial chiller equipment, real - time maintenance and customized servicing remain the keys to reducing corrosion and extending the service life. Only through scientific and reasonable maintenance measures can industrial chillers operate continuously and stably in complex industrial environments and provide reliable support for industrial production. When you plan to buy an industrial chiller, Hengde Company is your reliable choice. We offer high - quality products and professional services to meet all your needs.
Choose Hengde, Choose Perfect Industrial Chiller!