With the rapid development of the manufacturing industry, metal processing technology has been continuously improved. As an efficient and precise metal bending equipment, CNC bending machine has become an important tool in industrial production. This article will introduce in detail what is CNC bending machine, as well as its working principle, main components and application areas.
What is CNC bending machine?
CNC bending machine is a metal sheet bending equipment controlled by a CNC system. It is mainly used to bend metal sheets according to predetermined angles and shapes. Traditional bending machines rely on manual operation, while CNC bending machines control the bending process through computer programs, which improves processing accuracy and production efficiency.
The core of CNC bending machine is its CNC system, which can be used to accurately program and control key parameters in the bending process (such as bending angle, bending position, pressure, etc.). Compared with traditional manual bending, CNC bending machine has the following significant advantages:
1. High precision: It can achieve micron-level bending accuracy to ensure product quality.
2. High efficiency: Reduce manual intervention and increase processing speed.
3. Strong flexibility: can process metal products with complex shapes.
4. High degree of automation: reduce the difficulty of operation and reduce human errors.
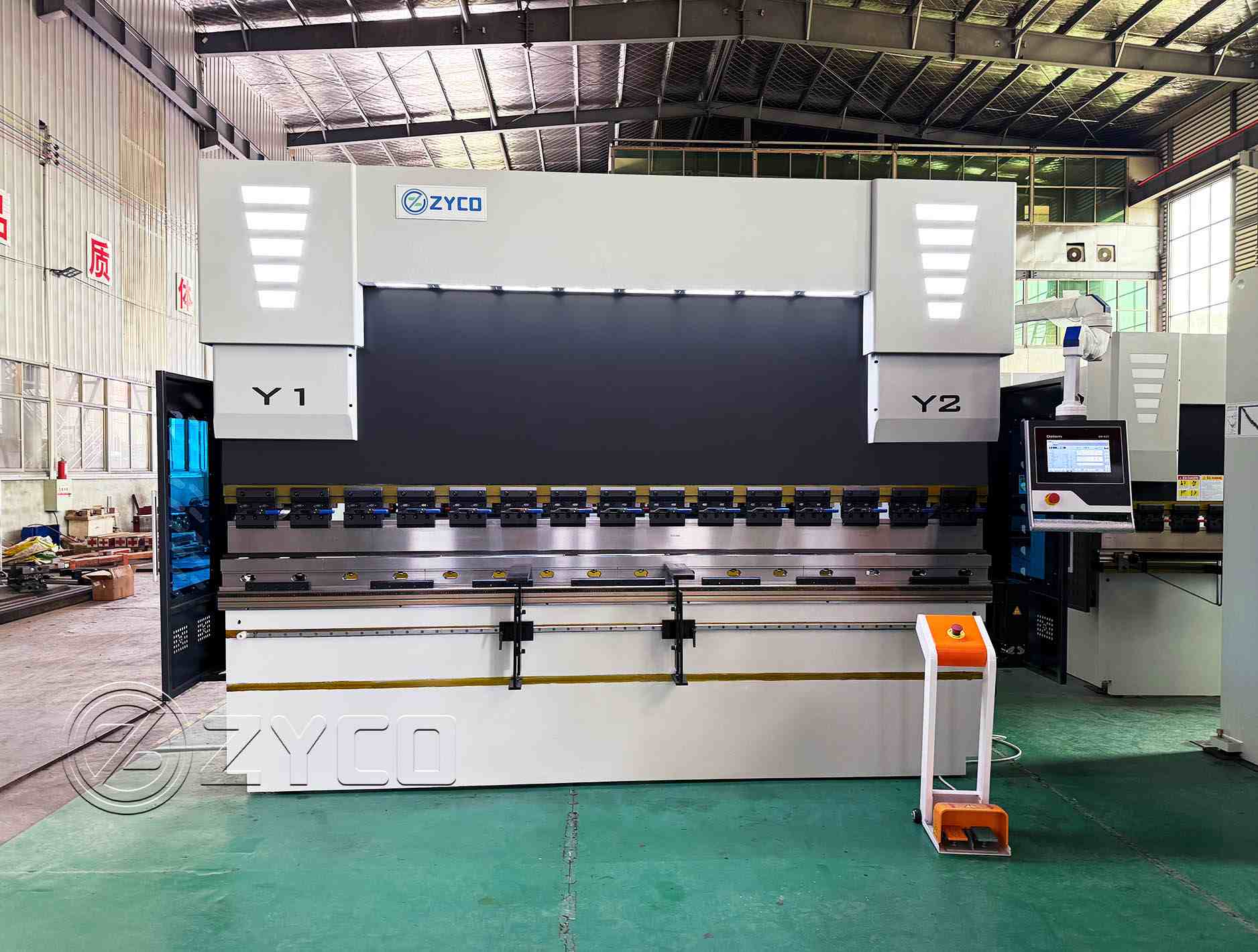
How does a CNC bending machine work?
The working principle of a CNC Press Brake mainly includes the following steps:
1. Programming and data input
The operator inputs the processing program for the bending machine through the CNC system. These programs are usually based on product design drawings and contain the following key information:
- Material and thickness of the sheet;
- Bending angle;
- Bending sequence;
- Tool selection (type of upper and lower dies).
Modern CNC systems support direct import of 3D design files (such as CAD files) and can automatically calculate bending process parameters, greatly reducing programming time.
2. Positioning and clamping
After the program is set, the back gauge system of the CNC bending machine will automatically adjust the position to fix the metal sheet in the appropriate position. The back gauge system is driven by a motor and can move accurately to ensure the accurate bending position of the metal sheet.
The clamping device fixes the sheet hydraulically or mechanically to prevent displacement during processing.
3. Bending action
The bending action is driven by the hydraulic system or servo motor of the bending machine, which drives the upper and lower dies to move:
Upper die: usually a wedge-shaped tool used to apply pressure to the metal sheet.
Lower die: usually has different notches to support the metal sheet and form the final bending angle.
The metal sheet is squeezed between the upper and lower dies, resulting in plastic deformation to form the desired angle and shape.
4. Feedback and adjustment
The CNC system monitors the pressure, angle and position during the bending process in real time and feeds back data through sensors. If an error is found, the system automatically adjusts the bending parameters to ensure that the final product meets the design requirements.
Main components of CNC bending machine

CNC bending machine consists of the following core parts:
1. CNC system (CNC controller)
This is the "brain" of the CNC Press Brake, responsible for receiving and processing operating instructions and controlling the operation of the equipment. Common CNC system brands include Siemens, Fanuc, etc.
2. Hydraulic system
Used to generate the pressure required for bending. The hydraulic system drives the piston movement through hydraulic oil, thereby driving the mold to complete the bending action.
3. Mechanical structure
Includes parts such as the frame, upper die, lower die and workbench. These components provide stable support and transmit pressure for the bending operation.
4. Back gauge system
Used to position the metal sheet to ensure the accuracy of the bending position. The back gauge system is usually driven by a servo motor and can achieve high-precision movement.
5. Sensors and feedback devices
Used to monitor key parameters in the bending process, such as angle, pressure and position, to ensure processing accuracy.
Application areas of CNC bending machines
CNC bending machines are widely used in the following industries:
1. Sheet metal processing: such as chassis, cabinets, home appliance housings, etc.
2. Automobile manufacturing: such as frame and body parts processing.
3. Aerospace: bending metal parts with extremely high precision requirements.
4. Construction industry: such as the production of metal curtain walls and steel structure components.
5. Home appliance industry: such as the processing of washing machines and refrigerator shells.
6. Kitchen equipment: such as ovens, rice steamers, etc.
Conclusion
As an important equipment for modern sheet metal processing, CNC bending machines have become the core tools in industrial production with their advantages of high efficiency, high precision and automation. Through the precise control of the CNC system, CNC bending machines can easily cope with complex processing requirements and provide strong support for the automation and intelligent development of the manufacturing industry.
In the future, with the integration of artificial intelligence and Internet of Things technologies, CNC bending machines will further enhance their intelligence level and bring more possibilities to industrial production.