The dynamic seal of a centrifugal pump is a sealing method that relies on the centrifugal force of rotating components, and it can be divided into two categories: back-blade seal and auxiliary impeller seal.
Back - blade seal:
(1) Structure: Blades are added to the rear cover plate of the impeller of the centrifugal pump, and these blades rotate in the opposite direction to the impeller. These blades are back-blades.
(2) Working principle: When the centrifugal pump is in operation, the rotation of the impeller drives the back blades to rotate together. The centrifugal force generated by the rotation of the back - blades will throw the liquid at the rear cover plate of the impeller to the outer periphery of the impeller, reducing the liquid pressure at the rear cover plate of the impeller and forming a low-pressure area. As a result, it is difficult for the high-pressure liquid at the impeller outlet to leak through the gap between the impeller and the pump casing to the low-pressure area, thus achieving the sealing effect.
(3) Advantages: The structure is relatively simple, no additional complex devices are required, and the cost is low; it can balance the axial force of the centrifugal pump to a certain extent, reduce axial movement, and improve the operation stability of the pump.
(4) Disadvantages: The sealing effect is relatively weak, and it may not be suitable for some occasions with very high sealing requirements; the presence of back-blades will increase the frictional resistance of the impeller, resulting in a slight reduction in the pump's efficiency.
Auxiliary impeller seal:
(1) Structure: It usually consists of an auxiliary impeller, auxiliary blades (also called back-blades), fixed guide vanes, and a shutdown sealing device. The auxiliary impeller is a small centrifugal pump impeller, which rotates coaxially with the working impeller of the centrifugal pump.
(2) Working principle: During operation, the liquid leaked from the working impeller of the centrifugal pump flows to the auxiliary impeller. The centrifugal force generated by the rotation of the auxiliary impeller forms a pressure head, which can resist the high-pressure liquid at the outlet of the working impeller from leaking out, thereby achieving the sealing purpose. When the pump is shut down, the dynamic seal of the auxiliary impeller does not work. The liquid pressure inside the pump is small, and the liquid leaked to the auxiliary impeller is sealed by the shutdown sealing device. For example, three oil seals and one water-blocking ring are used for sealing.
(3) Advantages: The sealing effect is relatively good, and it is suitable for conveying media containing certain impurities because the influence of impurities on the auxiliary impeller is relatively small; during the operation process, the centrifugal force generated by the auxiliary impeller can also play a certain stirring role to prevent the precipitation of the medium.
(4) Disadvantages: The rotation of the auxiliary impeller consumes a certain amount of energy, which will increase the power consumption of the pump; the processing accuracy requirements of the auxiliary impeller are relatively high, and the manufacturing difficulty is relatively large.
The dynamic seals produced by Anhui Changyu Pump and Valve Manufacturing Co., Ltd. are all made of fiberglass - reinforced plastic. Due to the relatively low density of fiberglass - reinforced plastic, when the back - blades rotate, at the same rotational speed, their moment of inertia is relatively small. This means that during the starting and stopping processes, the back - blades need to overcome less inertial force and can reach a stable operating state or stop more quickly. From the perspective of the sealing principle, the fiberglass - reinforced plastic back - blades are stable in performance when the centrifugal force generated by rotation throws the liquid at the rear cover plate of the impeller to the outer periphery. Moreover, the good corrosion resistance of fiberglass - reinforced plastic can prevent changes in the blade surface caused by liquid corrosion, thereby maintaining the formation of a low - pressure area stably for a long time and ensuring the sealing effect. For example, in the working condition of transporting a mixed solution of acid, alkali, and salt with a certain concentration, the fiberglass - reinforced plastic back - blades can maintain the sealing performance more effectively compared with metal back - blades and reduce the situation of seal failure caused by corrosion.
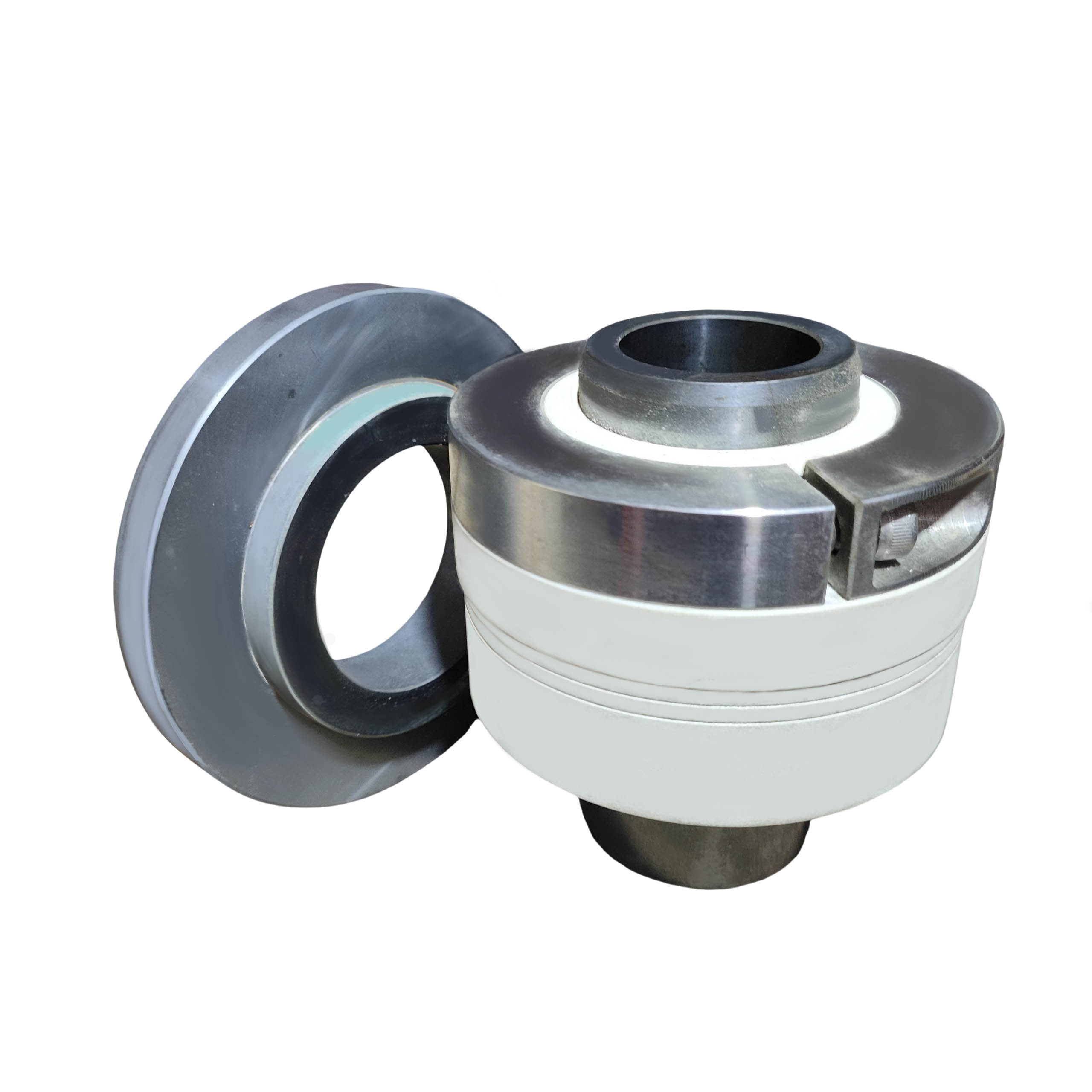
The mechanical seal of a centrifugal pump is a high-performance sealing method. The following is a detailed introduction:
Structural composition
(1) Rotating ring and stationary ring: The rotating ring rotates with the pump shaft, and the stationary ring is fixed on the pump body and remains stationary. They are the key sealing elements of the mechanical seal. They are usually paired with hard materials (such as tungsten carbide, ceramic, etc.) and soft materials (such as graphite, impregnated graphite, etc.). The end faces of these materials are finely ground with extremely high flatness. For example, in some high-temperature and high-pressure application scenarios, the combination of tungsten carbide and graphite is often used. Tungsten carbide has high hardness and good wear resistance, and graphite has good self-lubricating properties and chemical stability.
(2) Spring: The spring provides the axial pre - tightening force for the mechanical seal to ensure that the end faces of the rotating ring and the stationary ring are always in close contact during the operation of the centrifugal pump. There are various types of springs, including single-spring and multi-spring forms. The single-spring structure is simple, but the force is unevenly distributed; the multi-spring can make the force distribution more uniform and is suitable for high-speed centrifugal pumps.
(3) Sealing ring: It is used to seal the gaps between the rotating ring and the shaft, the stationary ring and the gland, etc., to prevent liquid from leaking from these parts. The material of the sealing ring is selected according to different working conditions. Common materials include rubber (such as nitrile rubber, fluorine rubber, etc.) and polytetrafluoroethylene. For example, when transporting acidic media, fluorine rubber sealing rings can be selected because of their good acid resistance.
Working principle
During the operation of the centrifugal pump, the spring force and the liquid pressure act on the rotating ring together, making the end faces of the rotating ring and the stationary ring closely contact to form an extremely thin liquid film. This liquid film has a sealing effect and can also lubricate and cool the end faces. Since the rotating ring rotates with the shaft and the stationary ring is fixed, the existence of the liquid film can reduce friction and wear when the two are in relative motion, when the pressure inside the pump changes, the change in liquid pressure will also affect the sealing force between the rotating ring and the stationary ring, thus ensuring the sealing performance under different working conditions.
Advantages
(1) Good sealing performance: The leakage of the mechanical seal is extremely small, which can effectively prevent the liquid inside the pump from leaking. It is very suitable for some occasions with strict leakage requirements (such as centrifugal pumps for transporting toxic, flammable, and explosive media).
(2) Long service life: The high-quality materials of the rotating ring and the stationary ring and the reasonable structural design enable the mechanical seal to operate stably for a long time under normal working conditions, reducing the trouble of frequent seal replacement.
(3) Adapt to various working conditions: It can adapt to complex working conditions such as high temperature (some mechanical seals can work in a high-temperature environment of several hundred degrees), high pressure (the pressure can reach several megapascals or even higher), and high speed (high - speed centrifugal pumps), and has good sealing effects for clean media and media containing a small amount of impurities.
(4) Low power loss: Since the liquid film between the rotating ring and the stationary ring plays a good lubricating role and the friction coefficient is small, compared with the packing seal, the power loss of the mechanical seal is lower, which is beneficial to improving the operation efficiency of the centrifugal pump.
Disadvantages
(1) Complex structure: The mechanical seal has many components, and the structure is relatively complex, with high requirements for design, manufacturing, and installation. For example, the parallelism of the end faces of the rotating ring and the stationary ring is strictly required, and a slight deviation during the installation process may affect the sealing performance.
(2) High cost: The high-quality materials of the rotating ring and the stationary ring are expensive. Coupled with the precision processing technology and complex assembly requirements, the cost of the mechanical seal is much higher than that of other sealing methods such as the packing seal.
(3) Sensitive to impurities: If the medium contains more solid impurities or particles, the impurities may enter between the end faces of the rotating ring and the stationary ring, scratching the sealing surface and causing the seal to fail. Therefore, there are certain requirements for the cleanliness of the medium.
The mechanical seals produced by Anhui Changyu Pump and Valve Manufacturing Co., Ltd. have good sealing performance, long service life, can adapt to various working conditions, low power loss, and high processing precision. With strict factory - out inspection, the superior performance of the mechanical seals is ensured.
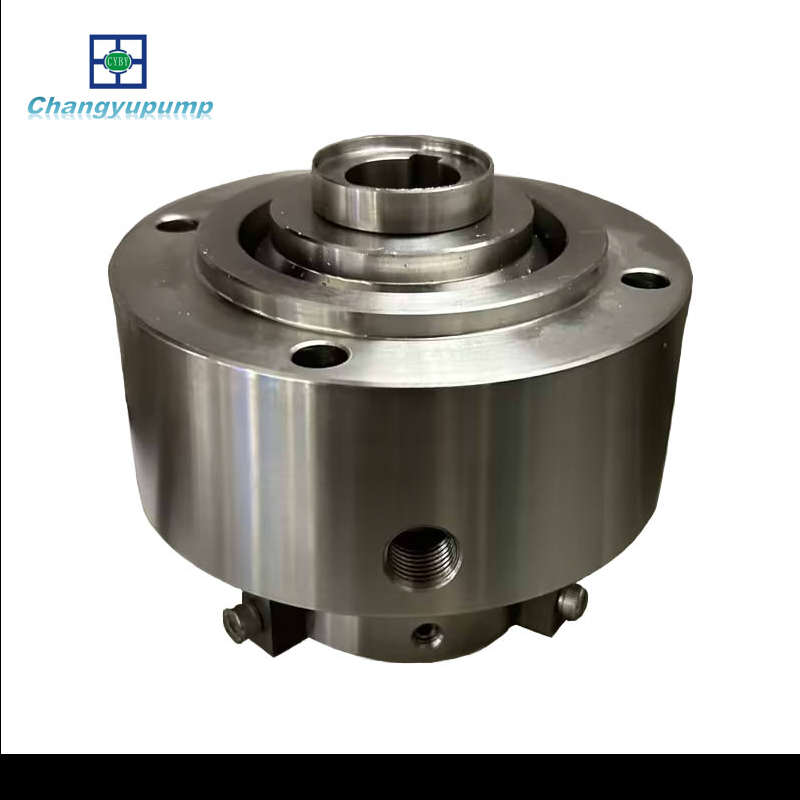